A rotogravura é um sistema de impressão encavográfico. Isto significa dizer que a área de grafismo (a parte da imagem que será impressa) está “escavada” no cilindro de impressão (a fôrma).
Muitas vezes, falamos sem perceber que a imagem está em “baixo relevo”, mas a verdade é que esse termo não faz sentido, uma vez que todo relevo está em um ponto elevado.
Este vídeo fantástico do gravador de cilindros Janoschka nos dá uma boa noção do processo de fabricação de um cilindro de rotogravura:
História e desenvolvimento
O século dezenove foi bastante produtivo em termos de desenvolvimentos, ideias e patentes na área de fotografia, fotoquímica e processos de produção de fôrmas (muitas pessoas chamam as fôrmas de “matrizes”, mas aqui estamos apenas respeitando a nomenclatura vigente nas normas da ISO que regulamentam o campo gráfico.
Henry Fox Talbot parece ter sido o primeiro a utilizar-se de processos fotográficos para criar imagens de meio-tom na produção de fôrmas de impressão, no ano de 1852. Uma patente francesa, datada de 1860, descreve inclusive uma máquina bobina-a-bobina muito similar a uma impressora de rotogravura moderna.
Mas foi uma colaboração entre o pintor, fotógrafo, caricaturista, ilustrador e litógrafo theco Karek Václav Klietsch com outro fotógrafo, Samuel Fawcett, que resultou no surgimento da Rembrandt Intaglio Company, no ano de 1895. Esta empresa produziu impressos de arte e, em 1906, ela propagandeou a primeira impressora de rotogravura multicolorida.
Desde então, a rotogravura não parou mais. Em meados de 1912, suplementos de jornais como o The Illustrated London News e o Der Weltspiegel eram impressos em rotogravura.
A rotogravura passou a dominar setores como jornais, embalagens flexíveis plásticas e de papel, envoltórios para cigarros, papel de parede, revestimento de pisos e outros materiais que simulam padrões da natureza como madeira.
O surgimento e o aperfeiçoamento da flexografia acabaram limitando, mais tarde, o crescimento da rotogravura – especialmente na impressão de embalagens flexíveis – em virtude dos lotes cada vez menores e uma maior segmentação de produtos, que dificulta a diluição dos custos dos cilindros, de maior durabilidade que as fôrmas flexográficas.
Características do sistema
O processo de impressão é direto. Isto significa que o cilindro, elemento responsável por transferir a imagem ao substrato – recebe tinta e toca o material diretamente – diferentemente da impressão offset, por exemplo, em que a imagem da chapa é transferida a um elemento intermediário, a “blanqueta”.
Este cilindro metálico fica imerso numa banheira com tinta e gira dentro dela. A tinta, arrastada com a revolução, é dosada com precisão por uma lâmina raspadora, que ao mesmo tempo em que faz com que a tinta preencha todos os alvéolos ou células gravadas que compõe as imagens, cor a cor, nos cilindros, também retira o excesso – deixando a área de contra-grafismo limpa.
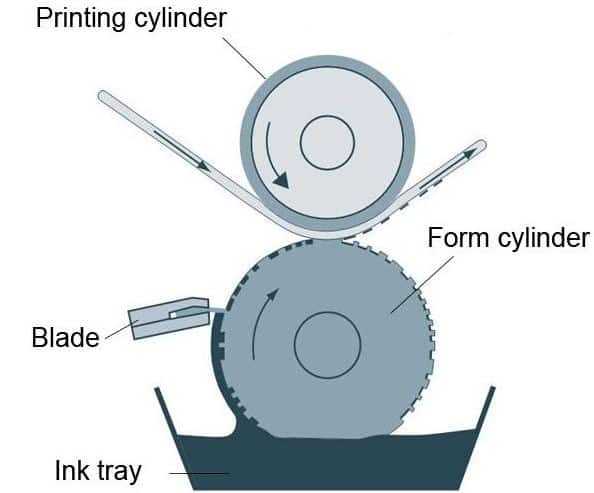
Um rolo de borracha pressiona o substrato para que possa receber a impressão, de forma suave e integral. Quando a tinta não sai completamente das células gravadas de um cilindro de rotogravura, ela gera um defeito clássico deste sistema – o “missing dot” – ou ponto “esquecido”, que também chamamos de entupimento, inversão do ponto, micro furo ou ponta de agulha (pinhole), dentre tantos nomes que se dá por aí, no cotidiano das empresas.
Para que esta impressão ocorra de forma precisa, a pressão do rolo de borracha, a sua dureza, as características da lâmina raspadora, a velocidade de impressão e a própria maciez e topografia do substrato são elementos críticos, que requerem dimensionamento e controle adequados.
A pré-impressão
Todas as imagens gravadas em um cilindro de rotogravura são formadas por alvéolos ou células, capazes de serem preenchidas de tinta e transportar esta película ao substrato. A quantidade de tinta contida nestas células corresponderá a diferentes densidades que se deseja obter na impressão.
As dimensões dos alvéolos, a sua geometria e as características de raspagem são fatores chave para a qualidade de impressão na rotogravura. O controle preciso da tinta e a competência do impressor cuidam do resto.
Aislan Baer, CEO da ProjetoPack e especialista em impressão
Existem diferentes métodos para produzir cilindros em rotogravura. Atualmente, o método mais usual é o eletromecânico – onde um equipamento chamado de “gravadora” utiliza um conjunto de diamantes especiais para perfurar, delimitar a profundidade da perfuração e “desenhar” a geometria mais otimizada para diferentes cores, lineaturas e características de reprodução desejáveis.
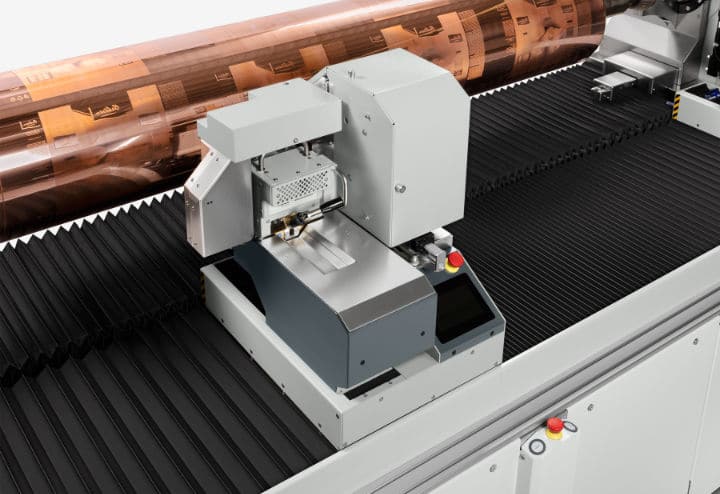
Esta necessidade de se traduzir as imagens – sejam meios-tons ou sólidos – em células, também determina uma das características visuais mais marcantes da rotogravura: a “serrilha” em traços ou linhas muito finas. Evidentemente que existem técnicas, equipamentos, configurações e até tecnologias (como o caso da gravação de cilindros a laser), capazes de reduzir ou mesmo eliminar esta característica, mas ainda é algo identificável na maioria dos impressos no mercado.
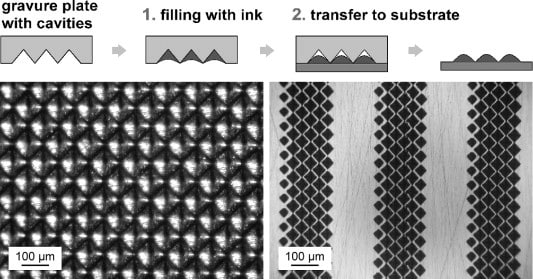
O mercado de rotogravura hoje
Apesar de não ser mais o auge da rotogravura, o sistema ainda é relevante em todo o mundo. Inúmeras pesquisas de mercado apontam que a indústria de rotogravura mundial fatura algo ao redor de USD 2,5 bilhões, podendo chegar aos USD 3 bilhões até o ano de 2030.
O maior fator restritivo da rotogravura é o aumento da exigência ambiental, especialmente na europa, para o uso do Cromo, elemento químico usado no processo de revestimento do cilindro de rotogravura para atribuir a dureza e resistência à raspagem.
Existem inúmeras empresas tentando reinventar os processos de confecção de cilindros da rotogravura, para estender o tempo de vida do sistema. A italiana Rossini, por exemplo, aposta numa tecnologia de um cilindro produzido com material polimérico especial, eliminando a necessidade do Cromo por completo.
No Brasil, existem convertedoras icônicas com capabilidades em impressão rotogravura, a exemplo de Amcor, Camargo Embalagens, Celocorte, Copobrás, Conver, Embalagens Flexíveis Diadema, Finepack, Gualapack, Toppan (Graffo e Inapel), Valgroup, Zaraplast e tantas outras.
A maioria das convertedoras de rotogravura do país possuem máquinas impressoras de 8 a 10 cores da plataforma RS (Rotomec e Schiavi, ambas empresas e projetos incorporados pela Bobst), da extinta Cerutti e até mesmo equipamentos nacionais da Profama e São José.
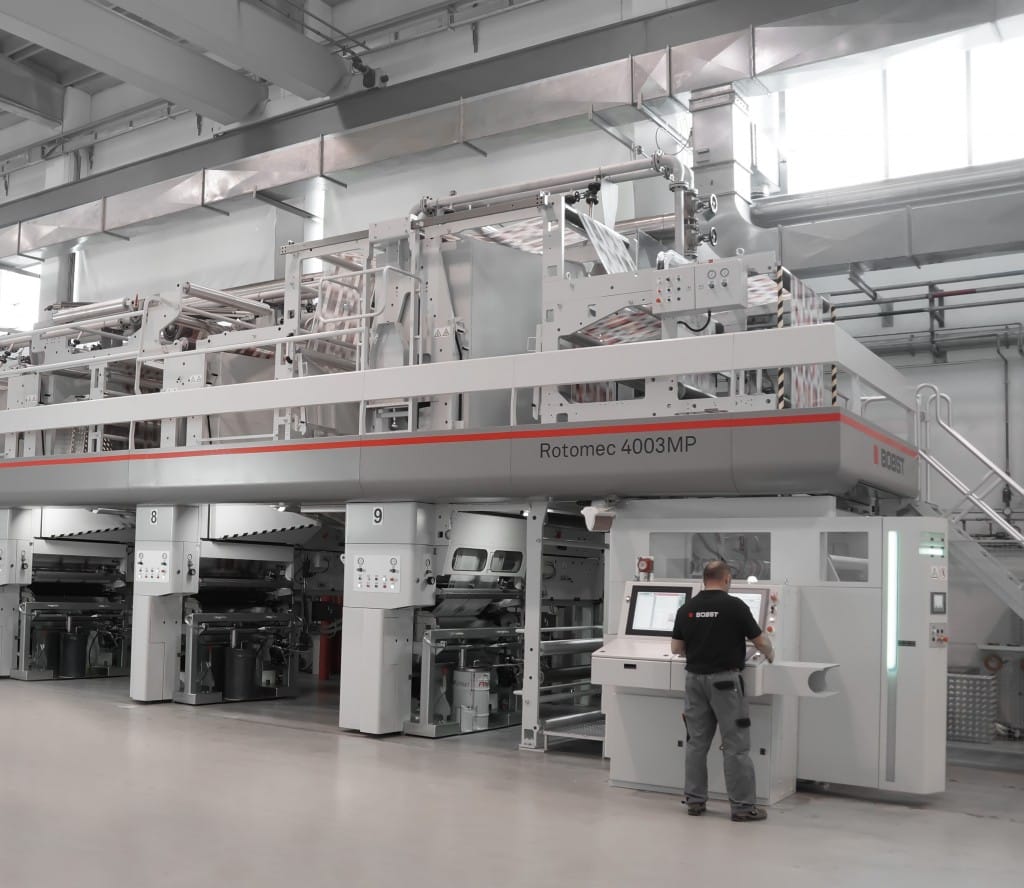
Algumas destas máquinas mais antigas são usadas na impressão de papéis para embrulhar e embalagens decorativas – aproveitando mais uma característica intrínseca da rotogravura: a impressão em “módulo contínuo” ou “sem emendas” proporcionada pelo cilindro de rotogravura.
Leia mais em nosso site: