É possível que esta seja a inovação mais importante da indústria de rotogravura da última década, com potencial para recuperar uma parcela importante do mercado absorvido pela flexografia ou, no mínimo, maximizar a lucratividade dos players deste segmento nos próximos anos.
Trata-se do Sistema “Ecograv”, apresentado pela companhia italiana Rossini S.p.A.: a primeira geração de cilindros de rotogravura sem o tradicional revestimento de cobre e cromo e, no entanto, prontos para receber a gravação em sistema eletromecânico.
Com um feito dessa magnitude, a Rossini S.p.A. confirma sua liderança tecnológica em todo o mundo, ao encontrar uma alternativa ao tradicional revestimento de cromo hexavalente dos cilindros de impressão, que mudou conceitualmente muito pouco desde os primórdios do processo de impressão em rotogravura.
A nova tecnologia é o desfecho de um extenso trabalho de pesquisa e desenvolvimento, com a curadoria pessoal de Felice Rossini, ao longo dos últimos dez anos.
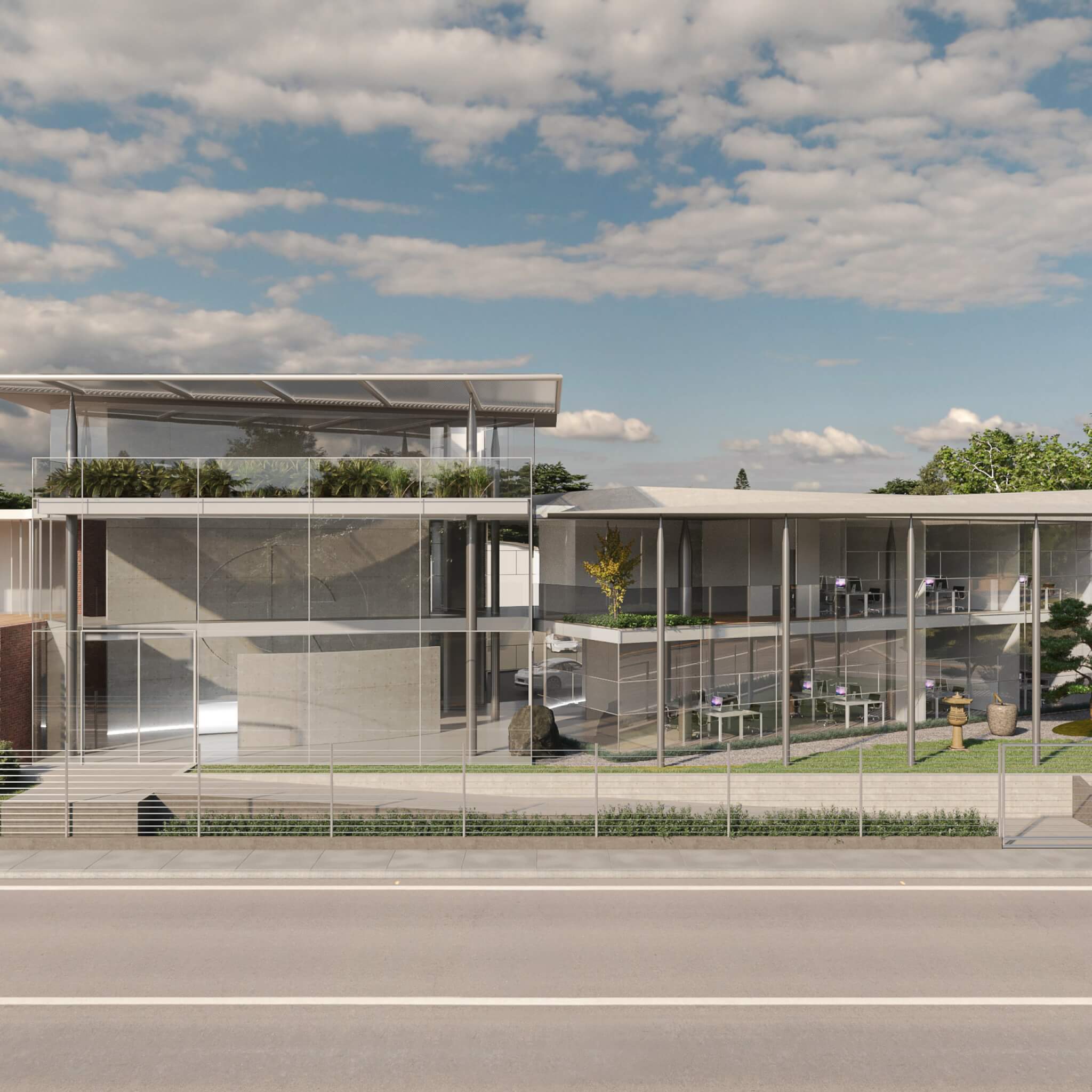
A rotogravura, especialmente nos últimos anos, perdeu uma fatia considerável de negócios a outros sistemas de impressão – em especial a flexografia – por conta dos malefícios à saúde e passivo ambiental resultantes do uso do cromo como revestimento do cobre após a gravação. Estima-se que autoridades ambientais competentes devem aumentar a pressão para restringir o uso do cromo em alguns anos, em processos galvanotípicos como o adotado na fabricação de cilindros de impressão rotográficos.
O sistema Ecograv substitui o revestimento de cobre e cromo atualmente em uso por um material especial: um tecnopolímero à base de poliuretano, que superou todos os testes de qualidade e maquinabilidade realizados ao longo do meticuloso processo de desenvolvimento industrial e que está apto a ser gravado eletromecanicamente.
A Rossini já construiu uma planta dedicada à produção do novo “cilindro de polímero”, composta por uma linha completa e automatizada que parte da matéria-prima a ser aplicada no cilindro e culmina no cilindro ou camisa prontos para a gravação. Neste ano de 2021, a nova planta piloto estará totalmente operacional no Centro de Tecnologia Rossini, de forma que clientes e prospectivos clientes possam conferir de perto os benefícios e prerrogativas da tecnologia.
O Grupo Gerosa – um parceiro de desenvolvimento de projetos e um convertedor de suma importância no mercado europeu, com plantas na Itália, Espanha e Romênia – foi o primeiro a assinar um termo de compra e compromisso, para receber o primeiro implante do Sistema Ecograv ICR. Um conhecido fornecedor de cilindros de rotogravura também apoiou o desenvolvimento e o projeto.
Conversamos com Flavio Losa, engenheiro da Rossini S.p.A., acerca do novo sistema.
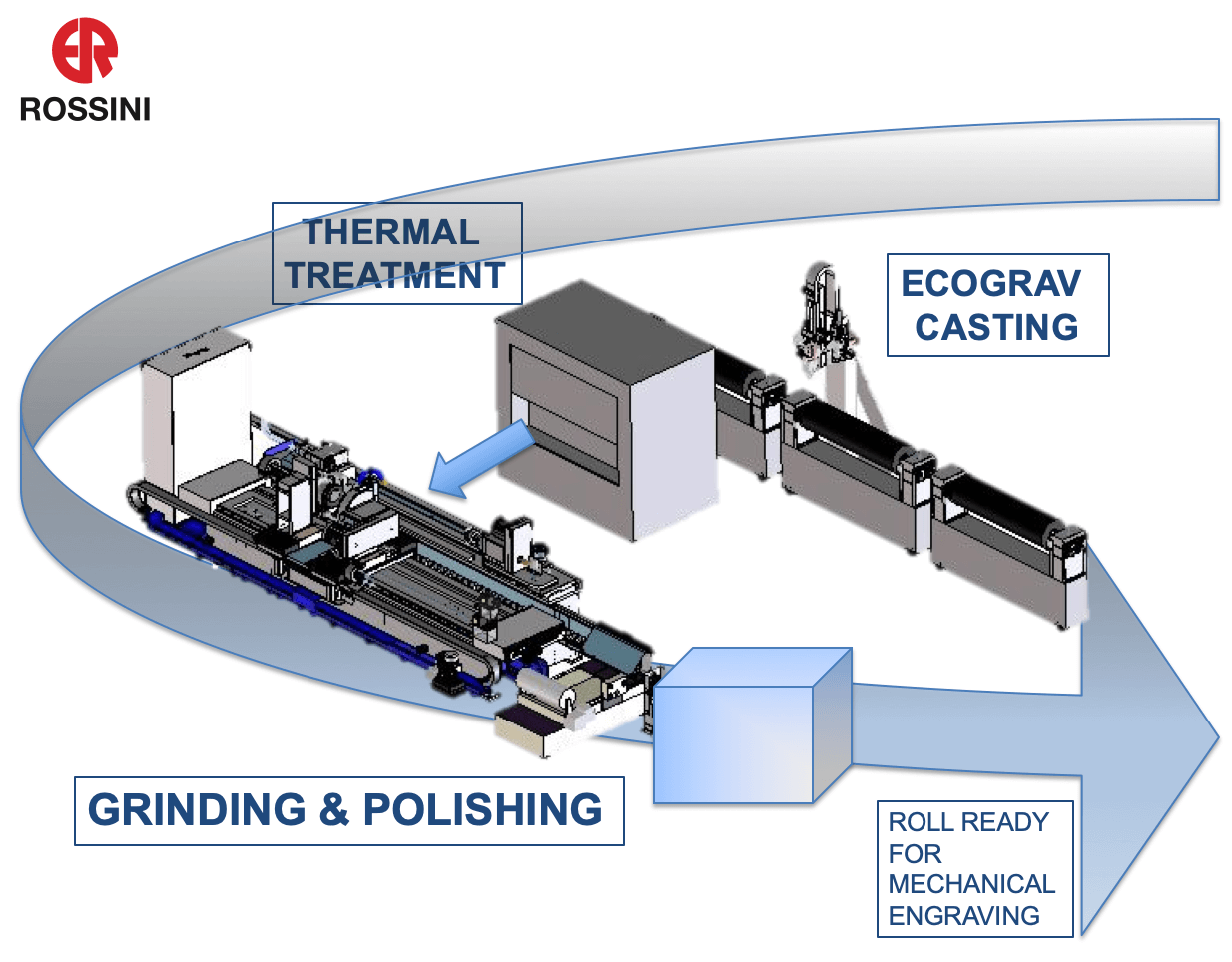
Na base do sistema, o cilindro
ProjetoPack: Doutor Losa, sempre acompanhamos e noticiamos as tentativas frustradas da indústria de rotogravura em reinventar o cilindro de cobre e cromo. Parece que a Rossini finalmente venceu este obstáculo. Poderia comentar algo a respeito dessa busca por um material alternativo?
Doutor Losa: O cilindro possui uma base de aço, que é revestido por cobre, gravado e finalmente, protegido por uma camada fina de cromo hexavalente. O cromo tem uma dureza superficial de 1000 a 1200 Brinell. Uma lâmina raspadora típica do processo de rotogravura tem dureza na ordem de 700 Brinell.
Esta relação de dureza entre o cilindro e a lâmina é um ponto-chave do processo de impressão. É justamente o cromo que, dentre outras atribuições técnicas importantes, estende a vida útil do cilindro e preserva as características da imagem gravada durante toda a impressão. O cromo 6+ (hexavalente) possui uniformidade superior, o que permite o gerenciamento e entrega de uma camada particularmente definida e constante durante a etapa de cromagem.
Depois de quase uma década experimentando, chegamos a um “tecnopolímero” a base de poliuretano (patente pendente), condutivo e, claro, retificável. O material apresenta um valor de aspereza superficial extremamente baixo, não muito longe do cromo e, sobretudo, pode ser gravado eletromecanicamente.
Este último dado é particularmente importante, pois até agora as experiências feitas em compostos plásticos consideravam a gravação a laser. Os equipamentos de gravação a laser presentes no mercado, porém, são muito poucos; quase todos os gravadores trabalham com sistemas eletromecânicos.
Nosso objetivo, portanto, sempre foi desenvolver um cilindro que pudesse ser gravado por todos, sem que seja necessário mudar a tecnologia. E conseguimos. Isso não exclui que num futuro próximo, Ecograv também não pode ser gravado com tecnologia laser.
ProjetoPack: Entendemos que a inovação não é apenas a descoberta de um novo material acessível e apto a ser gravado eletromecanicamente, correto?
Doutor Losa: além dos materiais, há grande aprimoramento nas técnicas de gravação, nos equipamentos envolvidos (que não impactam a saíde dos operadores e geram danos ao meio-ambiente) e no uso do produto. O novo polímero na base do Sistema Rossini Ecograv, uma vez removido, pode ser descartado exatamente como o plástico da coleta seletiva doméstica.
ProjetoPack: Para avaliar o desempenho do novo cilindro “plástico”, vocês envolveram um gravador e um convertedor, ambos muito bem equipados. Quais foram os resultados obtidos?
Doutor Losa: Primeiramente, fizemos os testes numa máquina impressora rotogravura monocolor, instalada em nosso centro de pesquisa e desenvolvimento. Imprimimos inicialmente algo por volta de 370 mil metros lineares de filme de poliéster 12 micron. Com velocidade de cruzeiro ajustada em 200 a 250 m/min e uma receita de processos padronizada – lâmina dosadora de aço inferior e tintas a base de acetato de etila – a impressão não apresentou problemas.
Para nossa satisfação e de nossos parceiros, obtivemos uma imagem de alta qualidade e definição, com densidade de tinta uniforme no curso de toda a tiragem. Mas não só isso: a constância do transporte da tinta está relacionada ao fato de as células (alvéolos) também se esvaziarem de maneira uniforme, rápida e sem grandes resíduos no fundo.
O ponto de impressão é melhor: perfeitamente redondo, sem quaisquer sinais de arrasto devido à lâmina dosadora. Claro que fizemos a curva de calibração para gravação, que nos permitiu obter um gradiente de tom absolutamente nivelado e, contudo, resultados equivalentes ou superiores aos de um cilindro de aço cromado convencional.
ProjetoPack: Qual o próximo passo nesta jornada?
Doutor Losa: Em breve, iniciaremos os testes mais complexos. A convertedora Gerosa irá reproduzir um impresso de 7 cores com todas as dificuldades mais desafiadoras: fundo sólido, código de barras, escrita em árabe, detalhes finos e grossos e um certo número de pantones. Um trabalho desafiador, que permitirá verificar a qualidade da impressão e do resultado em regime regular de produção.
ProjetoPack: Em que consiste a linha de produção do Sistema Ecograv?
Doutor Losa: A linha de produção consiste em uma estação onde ocorre a distribuição ou depósito do novo polímero, que é despejado no cilindro do usuário (estação de revestimento), seguida da parte da linha onde ocorre o tratamento térmico, que serve para estabilizar a estrutura cristalina do produto. Finalmente, é realizada a retificação e alisamento. O cilindro agora está pronto para a gravação.
ProjetoPack: Poderia descrever aos nossos leitores quais as principais vantagens um convertedor ou gravador de cilindros poderia esperar com essa nova tecnologia?
Doutor Losa: É um processo altamente automatizado e simples de usar, com estrutura modular, que gera um cilindro pronto para gravação eletromecânica e mostra a vantagem global da nova solução. Não só responde à necessidade de substituir o cromo hexavalente, que em breve será aposentado mundialmente, mas também surge como uma alternativa a um sistema de produção muito poluente e oneroso para se administrar em vários níveis – tais como a gestão da salubridade do local de trabalho e a própria eliminação de substâncias tóxicas usadas no processamento de fabricação convencional.
ProjetoPack: Poderia comentar algo acerca do aspecto econômico da solução?
Doutor Losa: O custo do cilindro de impressão obtido no sistema Ecograv será competitivo com o mercado atual e utilizará os cilindros dos convertedores em uso. Naturalmente, isso exigirá uma nova análise e gestão dos diâmetros, pois nosso aporte ou revestimento é de 2 milímetros. O inventário de cilindros de uma empresa contém geralmente milhares ou dezenas de milhares de peças, portanto não haverá dificuldade em encontrar o diâmetro correto para cada trabalho.
ProjetoPack: O investimento nesta planta também deveria ser inserido na análise ROI, não?
Doutor Losa: O discurso sobre ROI, como todos sabem, deve ser contextualizado e feito com precisão, dados e variáveis na mão. Toda a linha Ecograv System ocupa no máximo o espaço de um equipamento de galvanização e requer um investimento inferior ao de um processo tradicional, além de apresentar uma simplicidade de gestão que o torna um processo verdadeiramente “amigo do usuário e ambientalmente livre”.
Basta dizer que não exige autorizações para as emissões ou mesmo avaliações médicas periódicas da saúde do pessoal envolvido e, sobretudo, que elimina a priori todos os procedimentos de gestão de banhos galvânicos, águas residuais e produtos químicos.
É indubitável que este sistema tem potencial de transformar o setor e que as oportunidades, neste momento, estão apenas se descortinando às empresas interessadas em investir na nova tecnologia e diferenciar-se no competitivo mercado da rotogravura.
Thomas Bell, britânico detentor da patente 1443, datada de 1784 – a primeira máquina impressora rotogravura “moderna” – sentiria orgulho: o calcanhar de Aquiles do mais antigo e tradicional método analógico de impressão gráfica do mundo foi solucionado, dando lugar a um novo sistema, uma “Rotogravura 2.0” convergente com as necessidades ambientais e de segurança ocupacional que a sociedade espera.
Leia mais em nosso site:
Esko inaugura fábrica para soluções de gravação de chapas
One Response
Boa tarde senhores;
Parabéns aos estudiosos, pelo grande feito para a rotogravura este processo bastante antigo e que agora entra na era 2.0, sem poluir o meio ambiente e com certeza com muito mais qualidade.